Factory Settings: Santa Cruz teaches Dirt Rag how to build a wheel the fast way
Originally posted on June 7, 2018 at 5:00 amWhile at Santa Cruz headquarters this spring for the company’s new Blur and Highball launch, a few attendees were offered a tour of the Santa Cruz factory led by Santa Cruz CEO Joe Graney. The company operates closer to a boutique brand than the powerhouse that it is. Unlike many large bike brands, Santa Cruz is unique in that the company assembles all its bikes in-house and builds each of its carbon Reserve wheels at the factory. Walking through the factory, you quickly get the sense that Santa Cruz has followed cues from “The Toyota Way,” creating both an efficiently lean workplace and a positive working environment for its employees.

Toward the end of the factory tour, Joe said there was a surprise for us over by the wheel building area. I was excited to finally catch one of the wheel building machines in action. We watched Santa Cruz’s top wheel-builder, Keila Bauerlein, lace up a few wheels in under five minutes.
“Now, it’s your turn,” Joe said. We will each have the opportunity to lace up a wheel using the BMD semi-automatic lacing machine.
“So, how much do these machines cost?” someone in the group asked.
“They are about $30k a piece and we have three of them,” says Joe.
Huh? Wait, what? Years of “don’t touch that” embedded in my brain from my mother had me staring like a deer in headlights. And you want us to build a carbon wheel?
“These are going through quality control, right?” I asked, confused. Joe just smiled with a shit-eating grin as we stood there trying to turn on our cloaking devices and not be volunteered as the first media member to break the $30,000 piece of equipment.
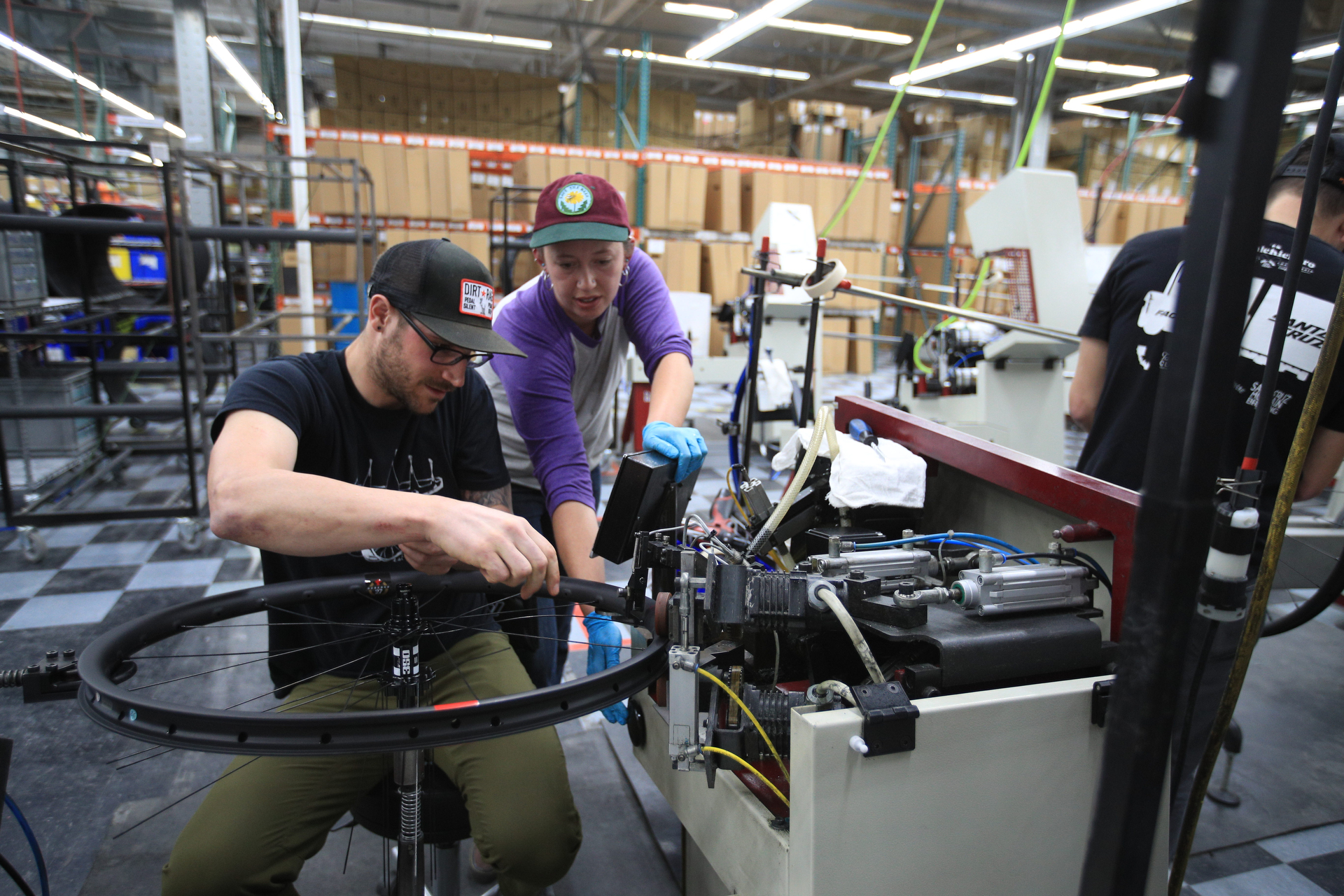
By the time my turn came around, the circle of gawking media personnel had thankfully decreased to half its original size. After watching a handful of others take a stab, my goal was to simply take my time and try to keep the machine happy. I nervously assumed my role in the captain’s chair. The lacing machine was already programmed with the dimensions of the hub/rim, the number of spokes, the lacing pattern, and the tension setting so the only thing left for the builder (me) to do was guide the spokes to the appropriate holes. Simple, right?
I placed the hub, pre-loaded with spokes, on a pedestal, drive side up. I held the carbon rim just above my lap with my right hand and guided the first spoke with my left to the appropriate hole. Nothing. In order to activate the lacing machine, you have to apply a small amount of pressure with your spoke to what looks like a record player stylus. Once pressure is applied, the machine shoots a nipple through the rim hole where it’s then pushed through and threaded to the spoke, all in a matter of seconds.

If done correctly, the machine audibly belches out a satisfactory blast of air. If not, the machine bellows in a fit of rage so that everyone around you knows that you just fucked up. Keila directed over my shoulder as I worked spoke by spoke around the wheel. Ok, so far, no double-threaded nipples as I approached the eight-minute mark—for a single wheel. By the way, the average time it takes an expert to lace up a wheel is only a minute and a half. Needless to say, I could only improve from here.
My input was finished once the wheel was laced up. We placed it on a track to be fed into the BMD truing machine, which fine-tunes the tension of each spoke. This machine is fully automatic and also costs double the price of the lacing machine. Watching the truing machine go through each spoke was soothing and put me into a trance similar to when watching the dancing flames of a campfire.
The wheel went through a series of measurements using lasers to find the baseline, and then a set of arms with spoke wrench fingers started making necessary tension adjustments to each nipple. The wheel spun back and forth continuously, the truing arms making small adjustments until it spun true.
If everything is good to go on a wheel, Joe explained, the machine will let the wheel roll down the “passed” track, but if there is something that needs to be addressed, the machine will fail the wheel and send it down a different track for the wheel to be addressed by hand. Mine passed and was spared the Veruca Salt treatment.
In order to ensure accuracy, every single wheel that comes off the line is finished and checked by a hand builder. The wheel is then put in a computer-like machine that provides a digital readout of the wheel dish and roundness, and once that is good-to-go, the wheel is inspected by a human one last time for any blemishes before getting valves and tape.

The freshly built Santa Cruz Reserve wheels were boxed for shipment to Dirt Rag headquarters for me to ride. It’s cool getting the opportunity to test a product that I played a (very small) part in building.
Subscribe today and don’t miss out on our long-term review of the Santa Cruz Reserve wheelset later this year.